LED Tester Also Calculates Resistor For Target Voltage
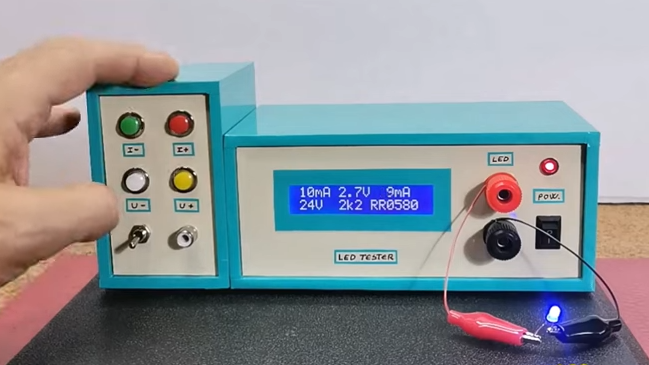
[mircemk] built a slick-looking LED tester with a couple handy functions built in. Not only can one select a target current to put through an LED, but by providing a target voltage, the system will automatically calculate the necessary series resistor. If for example the LED is destined for 14 V, this device will not only show how the LED looks at the chosen current, but will calculate the required resistor to get the same results on a 14 V system.
The buttons on the left control the target current and the voltage of the destination system. Once an LED is connected it will light up and the display indicates the LED’s forward voltage, the LED current, and the calculated series resistor value to obtain the same result at the selected target voltage. It’s a handy way to empirically dial in LED brightness values without needing to actually set up any particular test environment.
On the inside there’s little more than a handful of passive components, an Arduino, an LCD display, and a few buttons. This kind of tool reminds us of the highly clever component testers that hit the hobbyist scene years ago, showing what kind of advanced tricks a modern microcontroller is capable of with the right programming. (Here’s a look at how those work, if you’re interested in some deeper details.)
[mircemk] demonstrates his tool in the video, embedded below. We particularly like the attention he paid to the enclosure, giving it a very functional layout. It goes to show that when designing something, it’s never too early to consider enclosure and UI layout.