GymSoles ensure correct form and posture during your workout
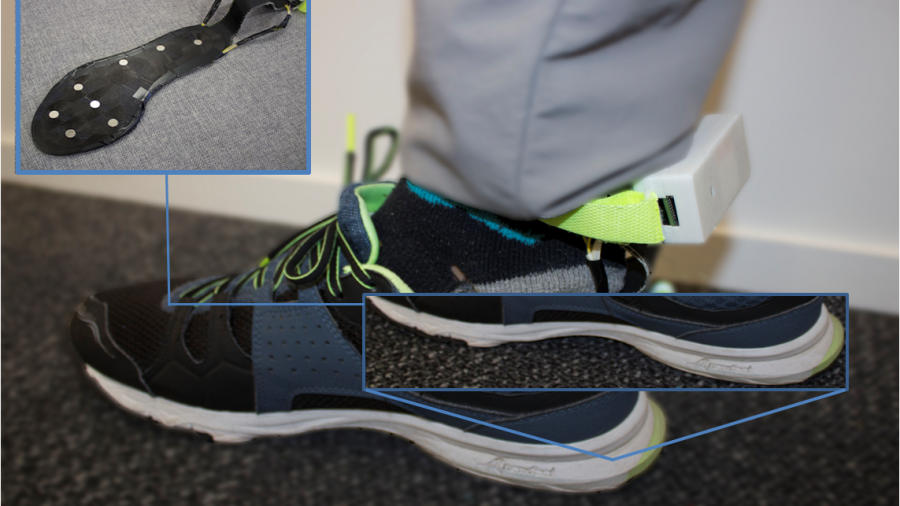
While you can get a very good workout on your own, it’s ideal if you have someone else watching over your form. This, of course, isn’t always practical, so researchers at the University of Auckland’s Augmented Human Lab have prototyped a wearable system called GymSoles to help.
GymSoles consist of a pressure-sensitive insole that is used to determine a foot’s center of pressure, and thus infer whether or not the participant is keeping the weights in the proper position relative to his or her body—perfect for exercises like squats and deadlifts.
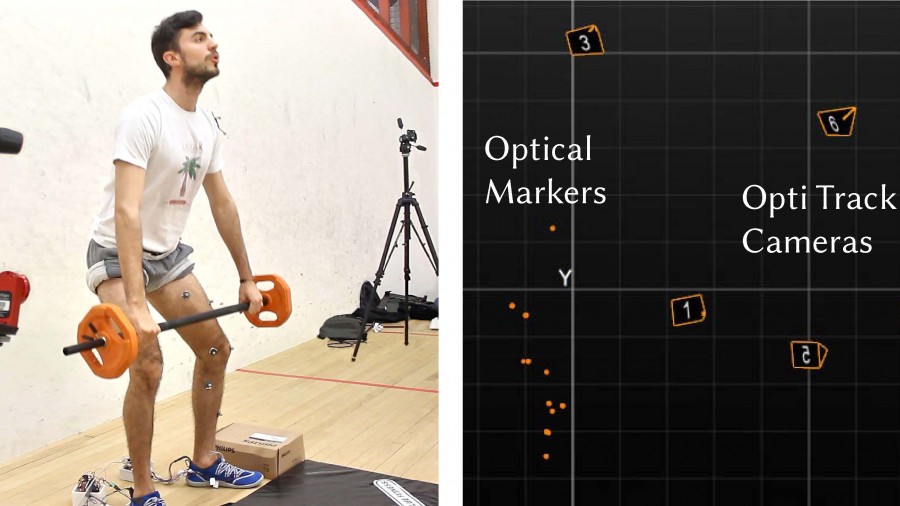
Feedback is provided visually as well as through tactile feedback via eight vibrating motors, allowing participants to modify technique without having to focus on a screen. A computer is used to control the device using an Arduino Uno with motor drivers and an I2C multiplexer.
The correct execution of exercises, such as squats and dead-lifts, is essential to prevent various bodily injuries. Existing solutions either rely on expensive motion tracking or multiple Inertial Measurement Units (IMU) systems require an extensive set-up and individual calibration. This paper introduces a proof of concept, GymSoles, an insole prototype that provides feedback on the Centre of Pressure (CoP) at the feet to assist users with maintaining the correct body posture, while performing squats and dead-lifts. GymSoles was evaluated with 13 users in three conditions: 1) no feedback, 2) vibrotactile feedback, and 3) visual feedback. It has shown that solely providing feedback on the current CoP, results in a significantly improved body posture.